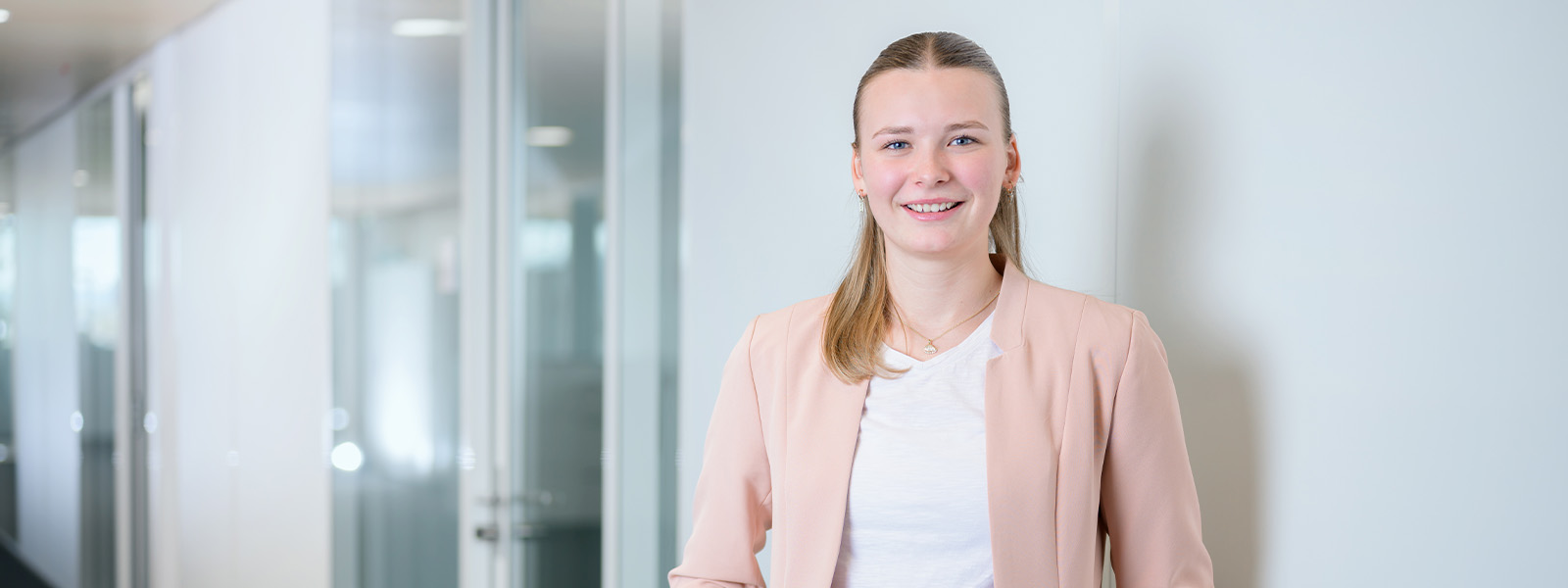
Sustainability
Ecological footprint
Energy supply and production
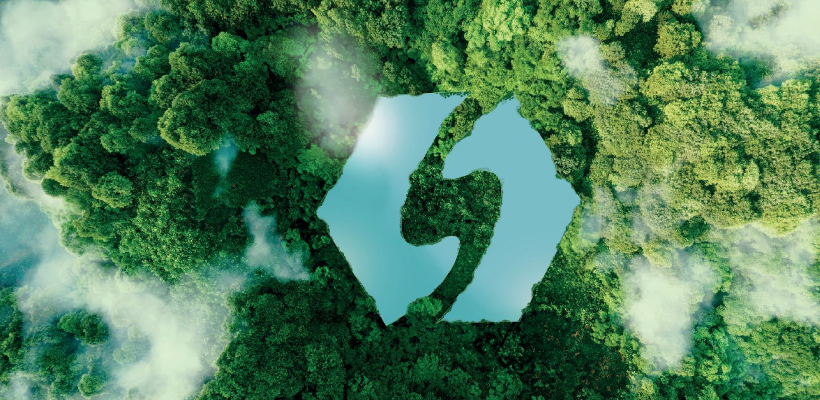
Facts
- annual electricity production of 440 megawatt hours in Frauenfeld
- The photovoltaic systems can cover 39% of our electricity requirements in Frauenfeld
- We heat with the energy of groundwater
- 40,000 liter tank for rainwater utilization
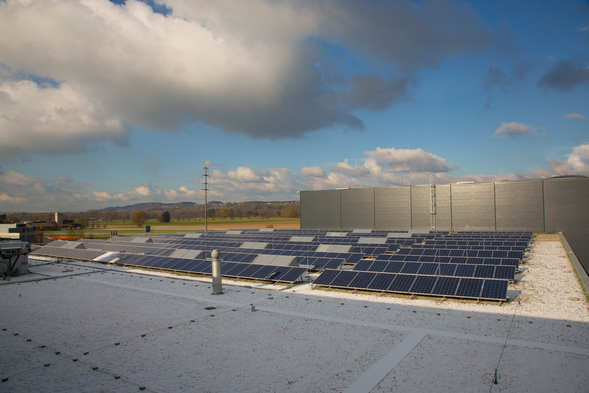
Solar plants
At the Swiss headquarters in Frauenfeld, a photovoltaic system with an installed capacity of 178 kilowatt peak is in operation on the roof of the production building, and we produce electricity with an installed capacity of 250 kilowatt peak on the extension building. This makes a total of 428 kilowatt peak. As a result of this new installation, we have been able to more than double the production of environmentally friendly electricity and we can therefore now cover at least 39% of our electricity requirements. In 2019, a photovoltaic system with an installed capacity of 124 kilowatt peak was installed at our site in Italy and the system in the Czech Republic produces electricity with a capacity of 250 kilowatt peak in late summer. The amount of electricity required at these two sites is very high due to the large number of CNC automatic lathes, and we are able to produce over 10% of the electricity required using the installations.
requirements thanks to the photovoltaic systems.»
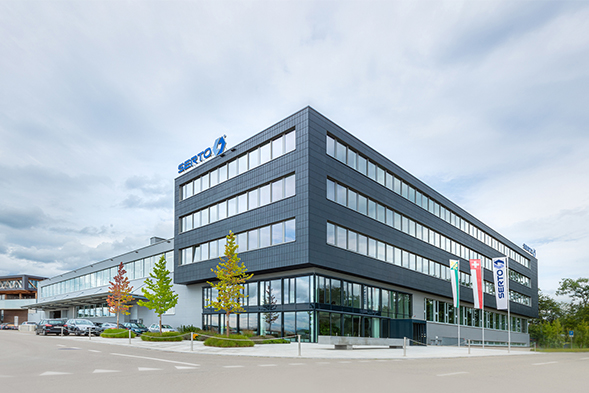
High-quality building envelopes
Long before the energy crisis, SERTO had already set the course and invested early in environmentally-friendly energy. The new building complex in Frauenfeld that is based on the Minergie standard was newly built in 2012. Minergie buildings are characterised by the very low energy requirements that they have and the highest proportion possible of renewable energy they use. A high-quality building envelope and systematic replacement of ambient air play key roles in this. Room heating is based on the principle of thermo-active building components: Heating pipes placed in the concrete core ensure a pleasant temperature. The floors, ceilings and walls of the building become active radiation surfaces, whereby the concrete mass acts as a thermal storage system and provides heat in winter and cools in summer.
systematic air renewal play key roles. »
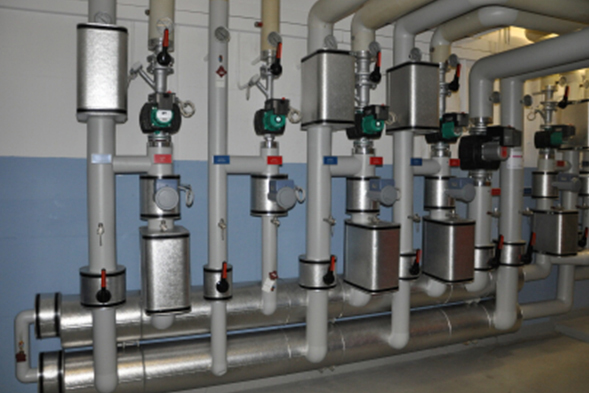
Heating using groundwater and using exhaust heat
From the roof, we are now moving into the depths of the cellar. We use neither oil nor gas for heating. Instead, we use the energy from the groundwater in the Thur lowlands combined with a heat pump-refrigeration unit. One pump extracts a maximum of 1,000 litres of groundwater per minute from a depth of 14 metres. At another location, the water is returned back into the ground with a temperature difference of up to 3°C. Furthermore, the central compressed air compressor produces the operational compressed air of 6 bar for the entire building. The exhaust heat from this is fed into the heating system via a heat exchanger.
neither oil nor gas, but the energy of the groundwater.»
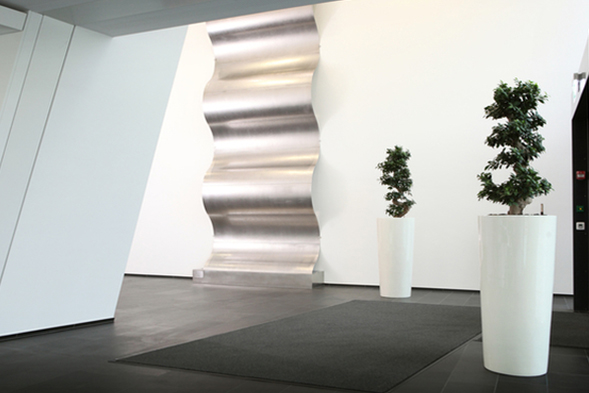
Using rainwater
our toilet facilities with flushing water, among other things.»
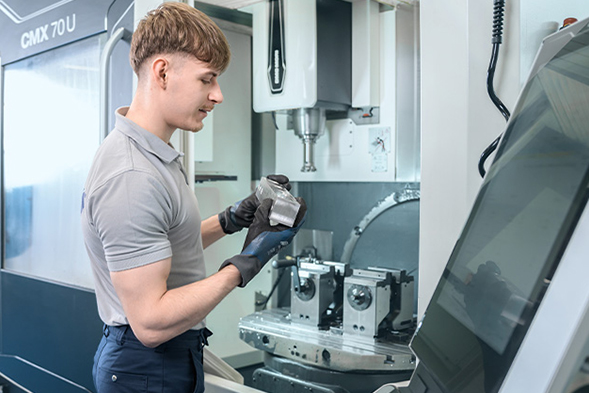
Production: Energy and raw materials
Making turned stainless steel parts in the Czech Republic and turned brass parts at our Italian site consumes a lot of energy. The CNC machines are replaced periodically, based on two objectives: To have cutting-edge technology at hand at all times, and to be able to operate our facilities with as little energy as possible. The stainless steel blanks for production at SERTO CZ have been optimised to produce less scrap when lathing them. You can’t plane a piece of wood without producing chips. Not only carpenters face that problem, but turneries like us also. We collect the chips left over from production and return them to the supplier, where they become a raw material for later reuse. Cutting something by chip removal also requires large quantities of oil. Centrifuges in both Brembate (IT) and Klatovy (CZ) recover this oil for purification and return to the production cycle. The same applies to the large volumes of water flowing through our ISO Class 8 cleanroom every day. This water cycles several times before it is contaminated wastewater, which the correct disposal channel guides on to treatment. A perfect circular loop.
Transport and logistics
We try to organise transports between our European sites such that unnecessary empty trips are avoided. One lorry a week commutes between the sites. Our packaging materials are sourced from recycling processes and our postal items are CO2-compensated. In order to minimise the amount of waste packaging, a growing number of regular customers can choose from multi-purpose containers or swap bodies for logistics. Production and consumers must free themselves from the idea of single use. All in all, companies must aim for efficiently organised cycles based on renewable energy. SERTO Group is constantly working on new concepts and pathways that will lead us to a true circular economy.
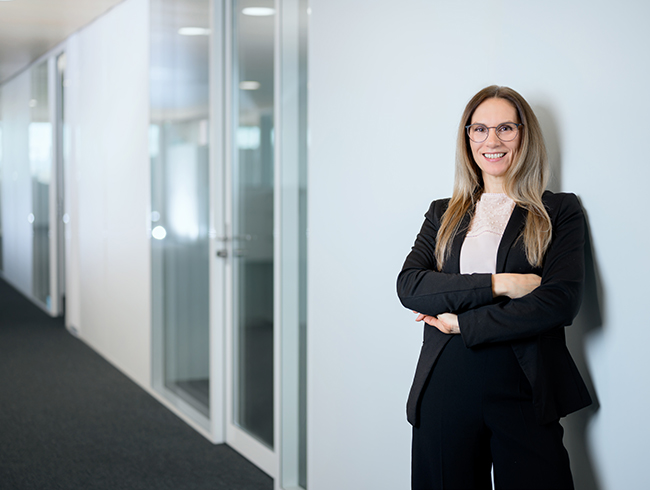
Your Contact
Have questions about our products or services? Our experts will be happy to help.