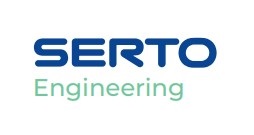
What our customers have to say about working with Project Engineering

Project process
A practical example of system optimisation
The graphics show a step-by-step system optimisation using a customer example. Costs, assembly time, the number of sealing points and the number of items to be processed changed in the course of the project to suit the customer.
Step 1
Initial situation: Distribution of a fluid from a conveyor unit to two containers. There is a regulating valve at the centre of this. The connection points and the valve are provided. And the desire to implement this solution with SERTO products.
Step 2
In order to guarantee the sealing of male connectors and a uniform screw-in height of the assembly, even after repeat assemblies, we have exchanged the conical male elbow connectors with cylindrical male elbow connectors with sealing edges
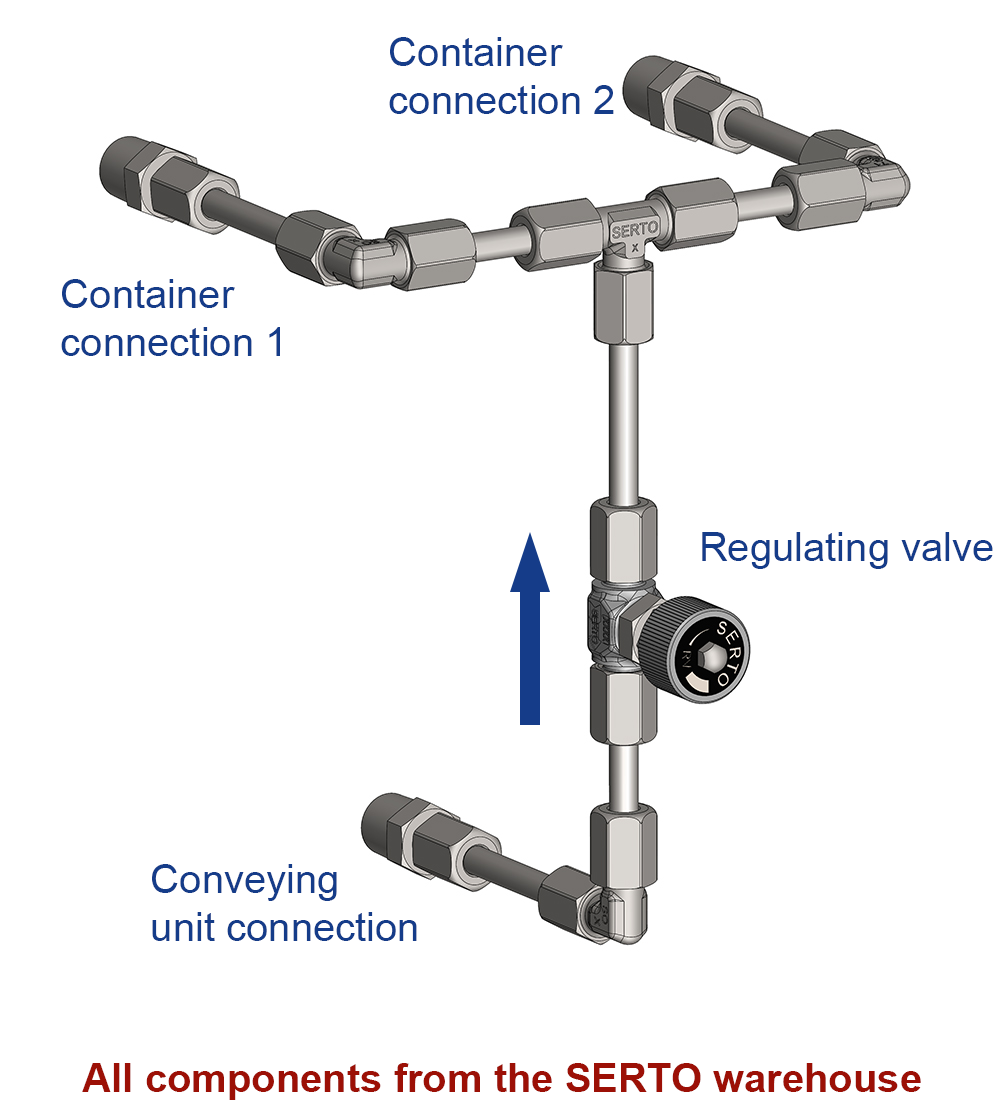
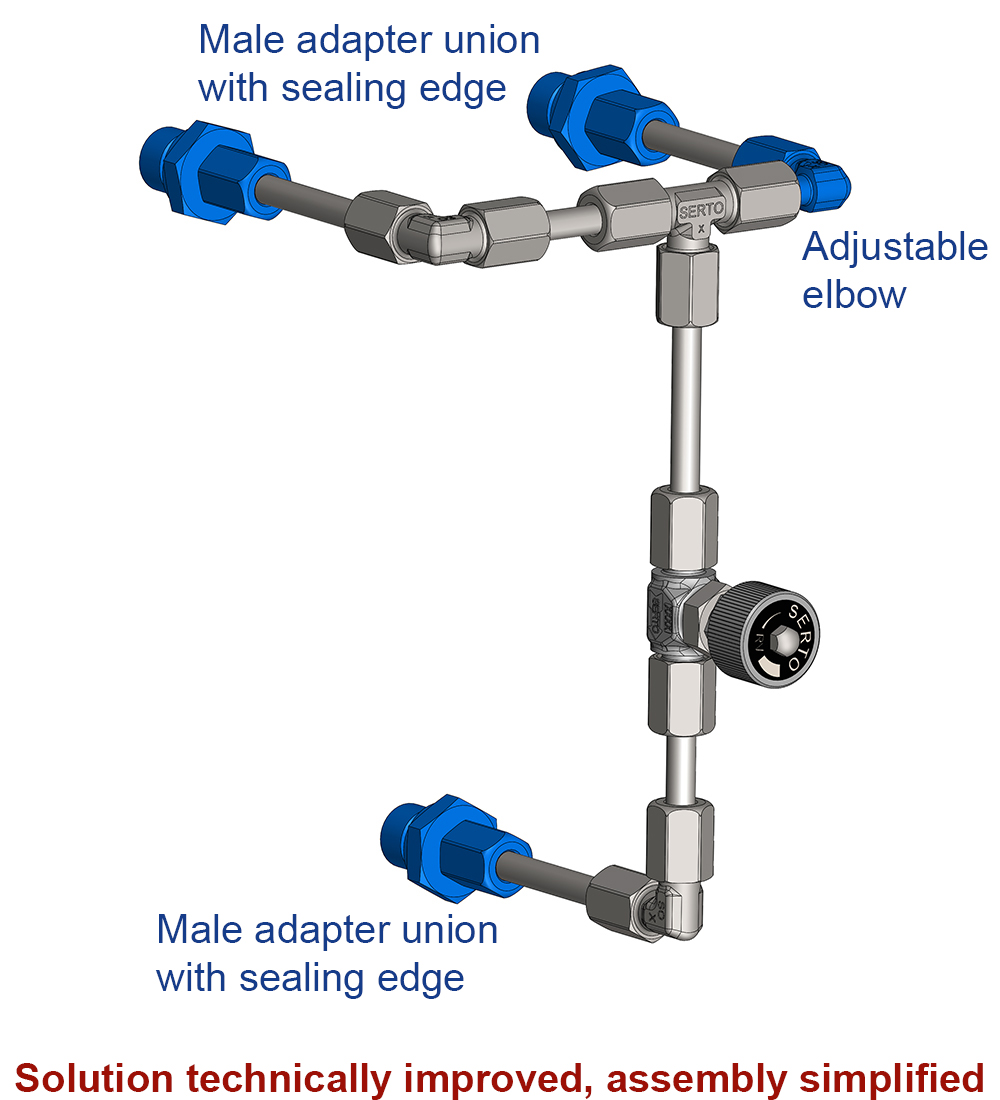
Step 3
Elbow fittings are replaced by bent tubes. This significantly reduces the number of sealing points.
Step 4
The final solution uses a solder assembly that also eliminates the central T union. The customer receives this assembly ready for installation.
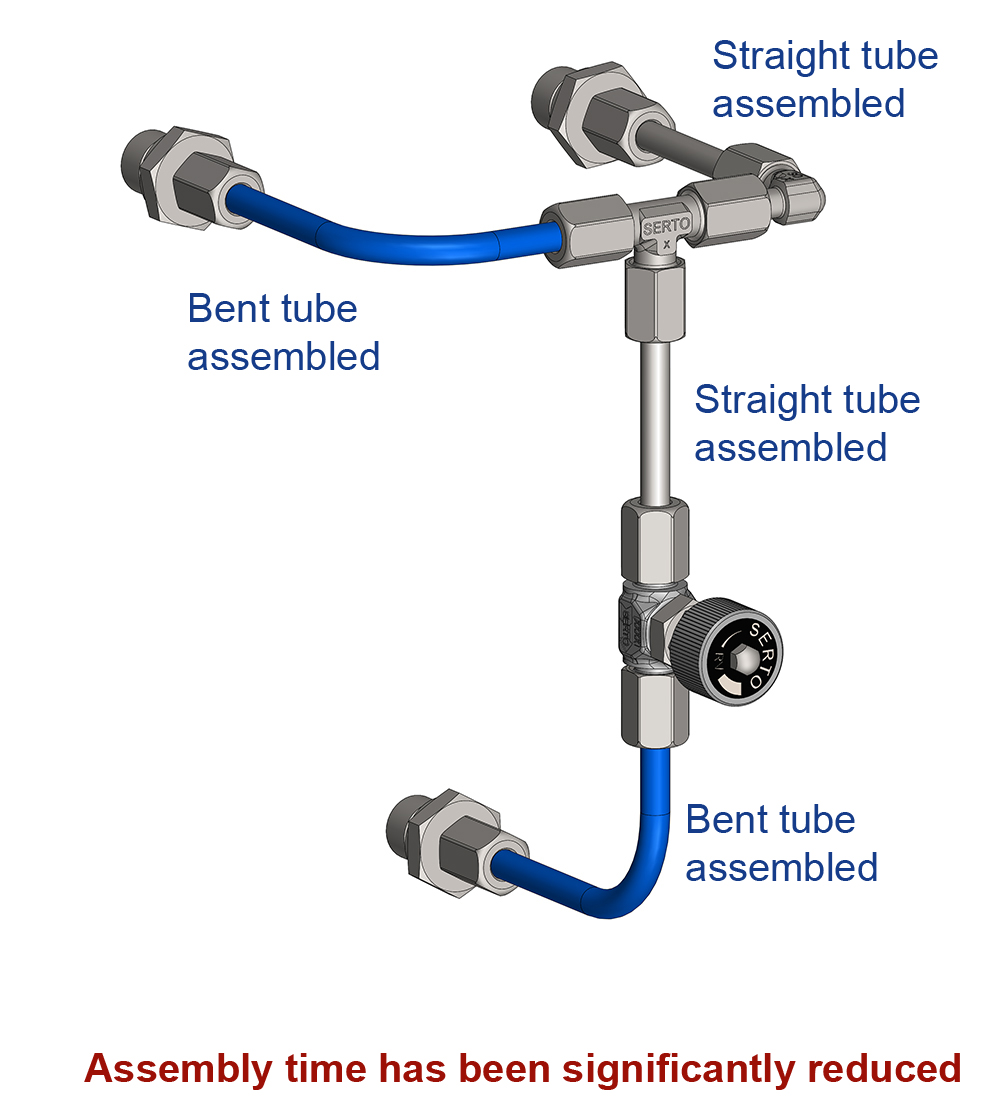
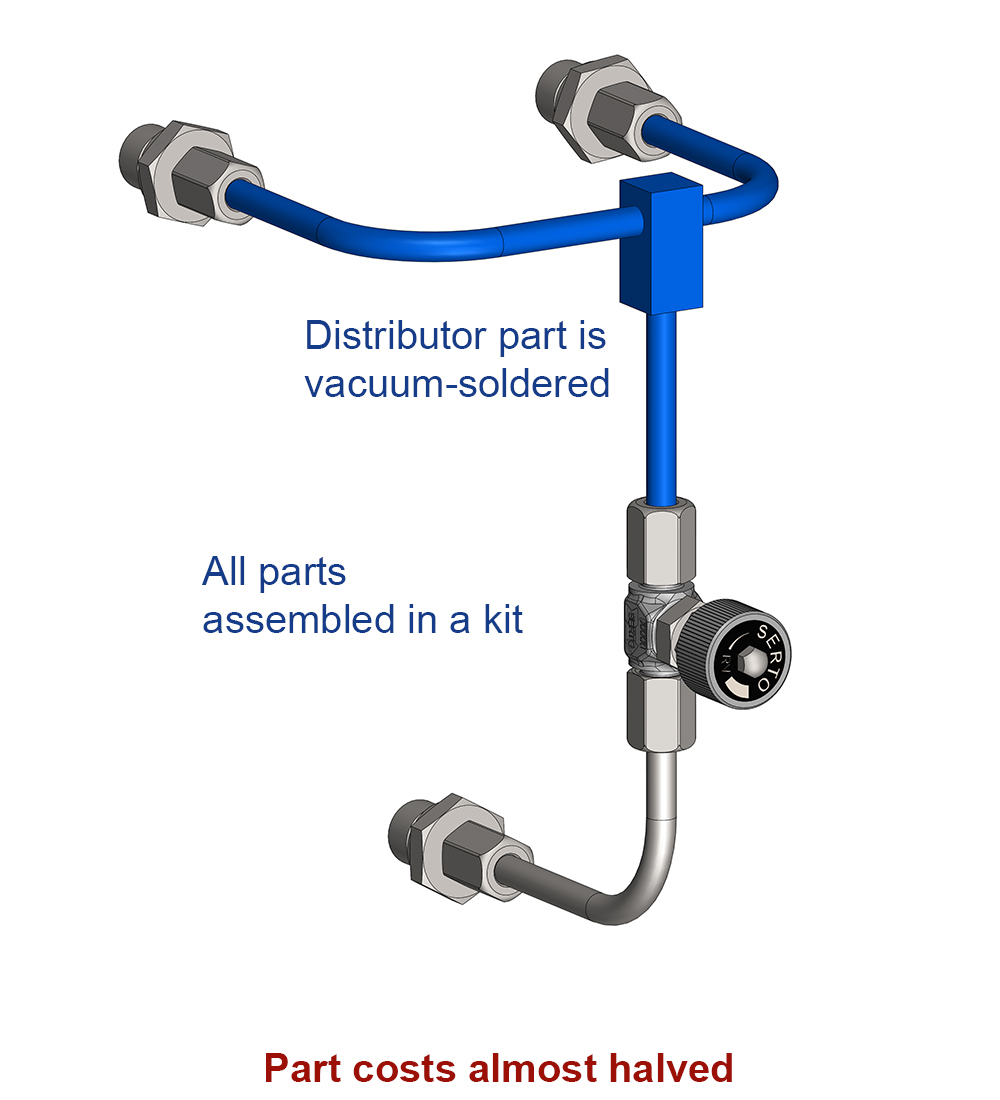